Setting up a cylindrical cell production line involves a series of precise and controlled steps to ensure the consistent quality and performance of the cells. Below is a detailed overview of the equipment and processes involved in making cylindrical cells, such as those used in lithium-ion batteries.
1. Electrode Preparation
Mixing
High-Shear Mixers and Planetary Mixers: These are used to mix the active material (such as lithium cobalt oxide for cathodes and graphite for anodes), binders (such as PVDF), conductive additives (like carbon black), and solvents (such as NMP for cathodes and water or ethanol for anodes) into a homogeneous slurry.
Parameters: Mixing time, speed, and temperature control.
Coating
Roll To Roll Coating Machine or Doctor Blade Coaters: Apply the slurry onto metal foils (aluminum for cathodes and copper for anodes) uniformly.
Parameters: Coating thickness, speed, and drying conditions.
Drying
Continuous Drying Ovens or Vacuum Dryers: Used to evaporate solvents from the coated electrodes.
Parameters: Temperature, airflow, and drying time.
Calendering
Rolling Press Machine: Compress the dried electrode layers to the desired thickness and increase density, enhancing the contact between particles and improving conductivity.
Parameters: Pressure, roller speed, and gap width.
Cutting and Slitting
Slitters and Laser Cutters: Cut the electrodes into precise strips suitable for winding.
Parameters: Cutting speed, precision, and edge quality.
2. Cell Assembly
Winding
Winding Machines: Wind the electrode strips and separator into a jelly roll configuration, which is then inserted into a cylindrical casing.
Parameters: Tension control, winding speed, and alignment accuracy.
Tab Welding
Ultrasonic Welders or Laser Welders: Weld current collecting tabs onto the electrode ends to ensure electrical connectivity.
Parameters: Welding power, duration, and alignment.
3. Electrolyte Filling
Electrolyte Filling Machines
Vacuum Filling Machines: Fill the cells with electrolyte under vacuum conditions to ensure complete wetting of the electrodes and separators without air bubbles.
Parameters: Vacuum level, filling volume, and rate.
4. Sealing
Crimping Machines
Crimping and Sealing Machines: Seal the top of the cylindrical cell with a cap, ensuring it is airtight.
Parameters: Crimping pressure, alignment, and sealing integrity.
5. Formation and Testing
Formation Chargers
Formation and Aging Chambers: Perform initial charging and discharging cycles to form the SEI (solid electrolyte interface) layer on the anode, which is crucial for cell stability and performance.
Parameters: Charge/discharge rates, cycle number, and temperature control.
Testing Equipment
Electrical Test Stations: Measure cell capacity, internal resistance, and other performance metrics.
Parameters: Accuracy, repeatability, and testing speed.
Safety Testing
Environmental Chambers: Test cells under various temperature and humidity conditions to ensure reliability.
Parameters: Temperature range, humidity control, and cycling protocols.
6. Final Inspection and Packaging
Inspection Machines
X-ray Inspection Systems: Check internal structure and electrode alignment.
Parameters: Resolution and inspection speed.
Visual Inspection Systems: Ensure external quality and labeling correctness.
Labeling and Barcoding
Labeling Machines: Apply labels and barcodes for identification and traceability.
Parameters: Placement accuracy and adhesion quality.
Packaging Lines
Automated Packaging Systems: Securely package cells for transportation and storage.
Parameters: Packing material quality and packaging density.
Key Considerations
Quality Control: Throughout the process, quality control checks are essential to ensure consistency and performance. This includes in-line inspection systems and periodic sampling for detailed analysis.
Safety: Given the potential hazards associated with lithium-ion batteries, safety protocols must be strictly , particularly during electrolyte handling and cell sealing.
Scalability: Equipment and processes should be scalable, allowing for the transition from pilot production to full-scale manufacturing.
Automation: High levels of automation help in maintaining consistency, reducing human error, and increasing production speed.
By carefully selecting and optimizing each piece of equipment and process step, a cylindrical cell production line can produce high-quality, reliable cells suitable for various applications, from consumer electronics to electric vehicles.
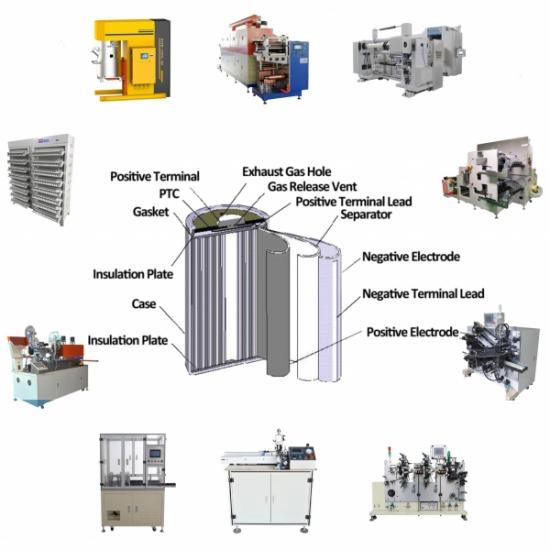